Insitu Line Boring - Machining Services
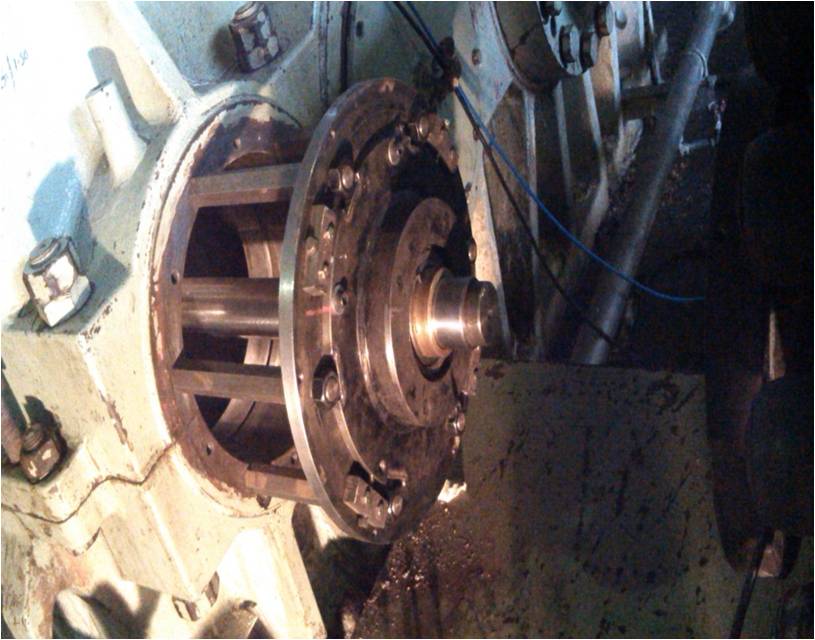
In-situ line boring is the process of re-boring more than one bore placed in the same axis. It's a single point tool machining process to ensure the bores retrieved from wear and tear without taper and ovality. In Situ Line Boring is needed for the bores during the maintenance process where the cylinders and rollers are rotating. The newly machined bores results in improvement in parallel running of cylinders and reduced noise & vibration of the equipment. In-situ line boring helps in keeping your plant running efficiently and safely.
Arudra's In-situ line boring machines save time and money by doing repairs on-site and in-place. We can provide required surface finish. Arudra is equipped with a full line of In-situ line boring machines that can handle bores 120 mm to 500 mm in diameter and the bores placed between 3 meters length and larger upon request.
Facility Available:
- Machining range from ø120mm to ø500mm and width of bore 500mm max
- With bearing housings mounted in the job or Steady rests for individual setting
- Length between the bores can be 3 meters max
- Single Point tool cutting process
- Electrical Operated)
- Below 0.1 mm Ovality and Taper
- Below 1.6 Ra Surface finish
Operation
- The housing assembliesare first mounted to front and back end of faceof the to-be-machined area.
- The boring bar is inserted into the housing such that it passes through the job and rests on the housing fit on the back.
- Then the motor is attached to the boring bar.
- The tool holder is fixed on the boring bar. Also, the single point cutting tool is fit on the holder.
- The housing assembly is checked for run-out and face-out.
- The machine is started after preliminary study is completed. The job is machined with the help of a special purpose feed machine.
- Once a particular depth is removed the tool holder is set to its original position and the steps are repeated.
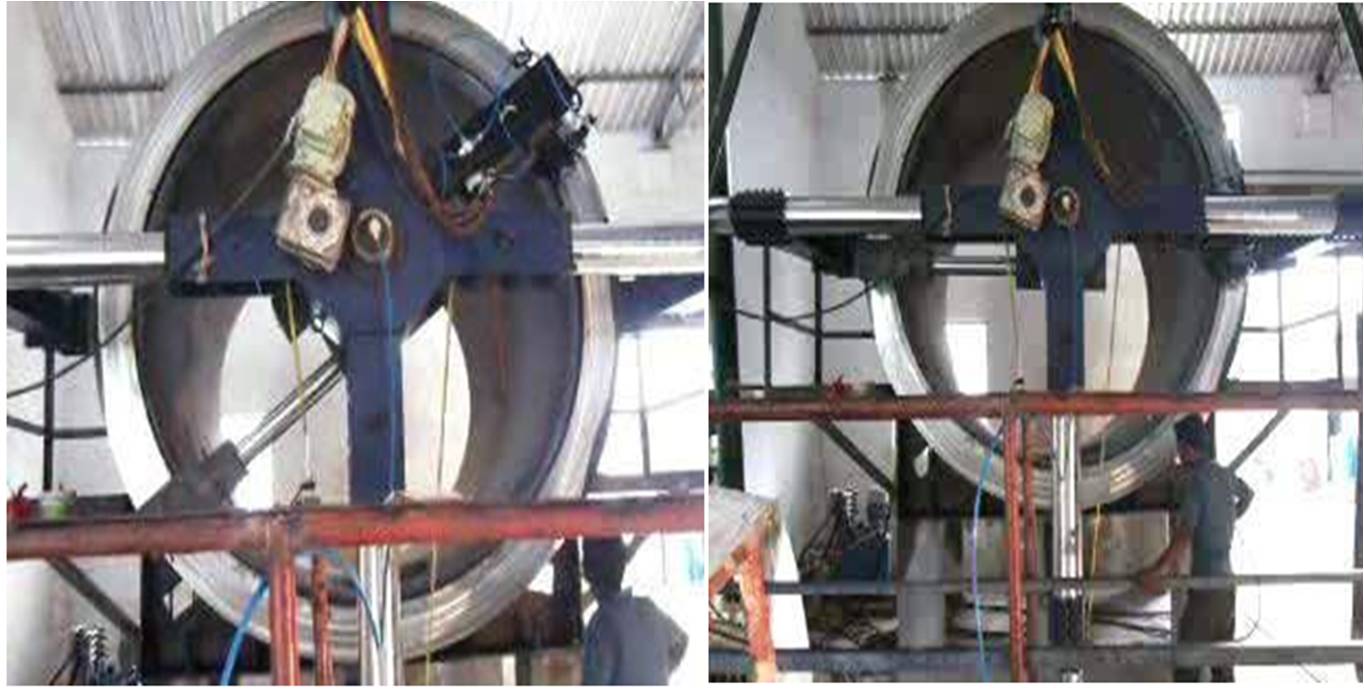
In-situ Flange Facing / Milling services
In-situ flange facing is the process of resurfacing flanges by machining to ensure a perfect seal when assembled
The newly machined surface then allows for an improved seal.
In-situ flange facing helps to keep your plant running efficiently and safely
Arudra In-situ flange facers save time and money by doing repairs In-situ and In-place.
Arudra In-situ flange facing machines are equipped with options like milling head, grinders or single point tool depending on the job to be performed
We can provide any type of surface finish as required.
We are equipped with full line of In-situ flange faces that can handle sizes ranging from 50 mm to 3000 mm in diameter and larger diameter upon request.
LINE BORING INSPECTION PROCESS
1. Consistency of the finish is measure using a Roughness meter.
2. The size of the final bore is also measure. An internal bore gauge is used for this purpose.
3. A well-documented report, detailing the summary of all the tubes inspected will be submitted to the customer later.
Areas of operation
Raised Face Flanges, Flat Face Flanges, RTJ Flanges, Re-Face Valve Seats & Compressors, Lens Ring Flanges, Tube Sheet Re-facing in Heat Exchangers, Shells, Man Ways, Pivot Bearing Faces on Heavy Equipment, Turbine Casings, Pressure Vessels, Process Reactors, Coupling Flanges, Hand Holes, Ring Groove, Diesel Engine Liners, Engine Block Landing Surfaces, Slewing Ring Landing Faces, Leaking Mating Surfaces, Pump Bases, Crane Pedestals, Channel Heads, Swicel Ring Flanges etc.
All machining is done to industry standards and specifications.
Line Boring by Arudra
Line boring takes time, particularly if you have to dismantle the machinery for transportation to a work shopWe do line boring Onsite
We provide In-situ line boring services from 100 mm to 5oo mm diameter with multiple bores